My senior capstone project was a joint collaboration project with Dr. Josh Kogot and the Naval Sea Systems Command (NAVSEA). The goal of the project was to design a 3D printer with the following requirements:
- Solar Powered
- Collapsible
- Portable
Dr. Kogot and his team at NAVSEA were exploring different ways to quickly produce parts "in the field" where a reliable source source of energy was not guaranteed, storage space was limited, and equipment was carried over long distances. The parts printed could be used for a range of applications from drone propeller and guard components to synthetic biological lattices.
The project started with many rounds of high level ideation. What physical form and shape would our device take? What essential mechanisms would meet the requirement?
As those questions and sub-questions started getting addressed, our team began developing prototypes to bring ideas in our head to physcial and tangible objects. When holding the first physical models, more clarity and direction on where to take the project arose. Accordingly, the challenges that we would face and need to address also became clearer as we moved forward.
The first phase of prototyping started with exploring different types of 3D printers. In today's day and age, there is a plethora, from resin based printers, traditional PLA/ABS printers, XYZ-Axis actuation, and Delta/Polar Coordinate systems to name a few. In order to incorporate the "portability" and "collapsibility" features our team also explored other machines in the world that also do these things. Construction Cranes interestingly became a big influence in their ability to handle torque and dynamic movement along with it's own assembly and transport between construction sites. With this idea we built some prototypes:
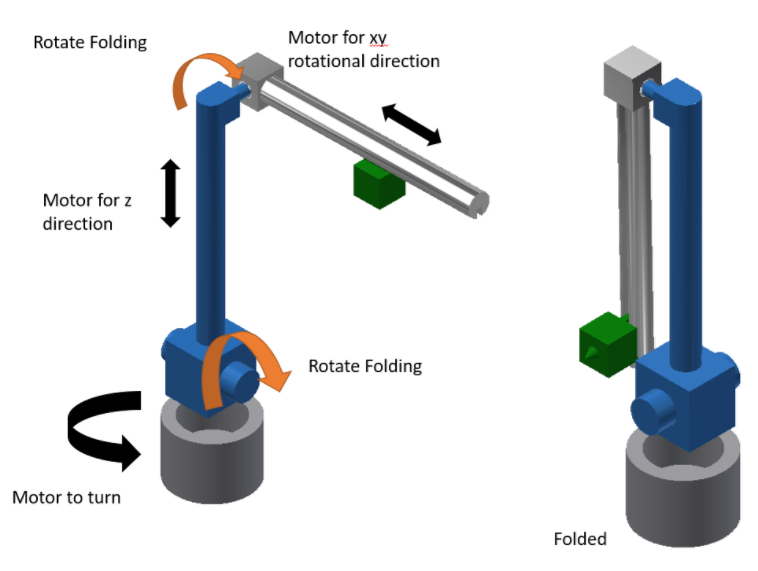
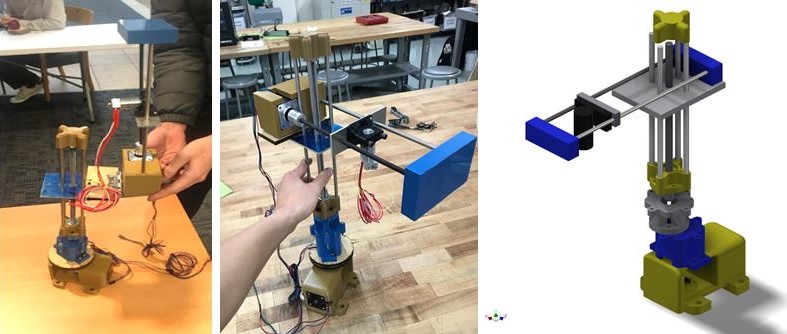
With our first prototype showing promise, the team continued to refine the design. We implemented better support structures, a new plastic extruder, and better folding mechanisms. We were also now moving from having individual software to manually control motors to integration with open source 3D printer communication software. It was the coolest feeling to finally see the ideas and concepts come to life and perform:
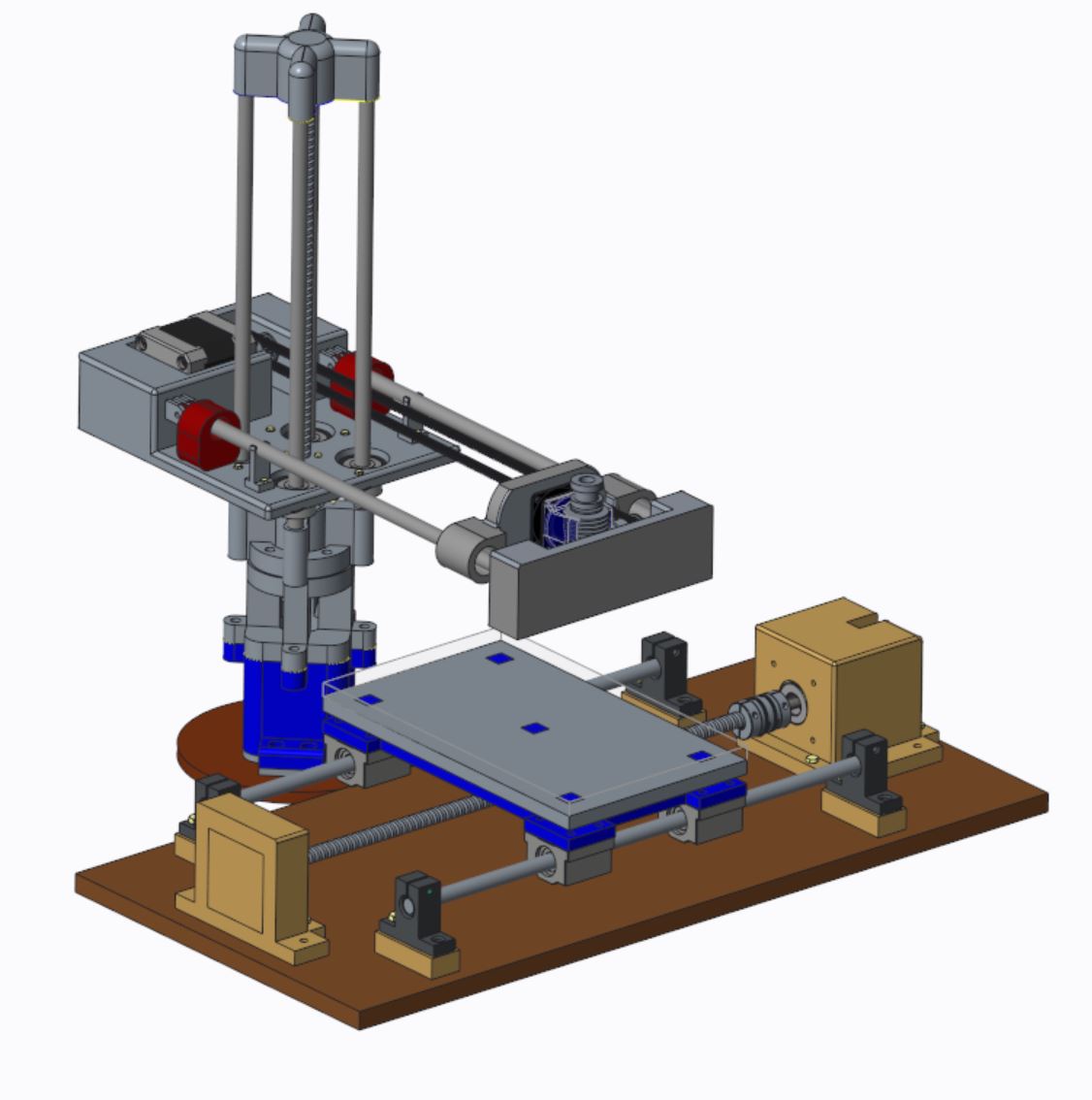
By the end of this 6 month journey, our team went from whiteboard ideas and napkin sketches to a full functioning prototype that printed out our first object. It's always crazy and amazing to look back on the journey of buidling something from concept to creation. You remember the late nights turning into early mornings, the struggle of failed prototypes, but at the end it's really cool to see something you and your team worked hard on finally come to fruition.
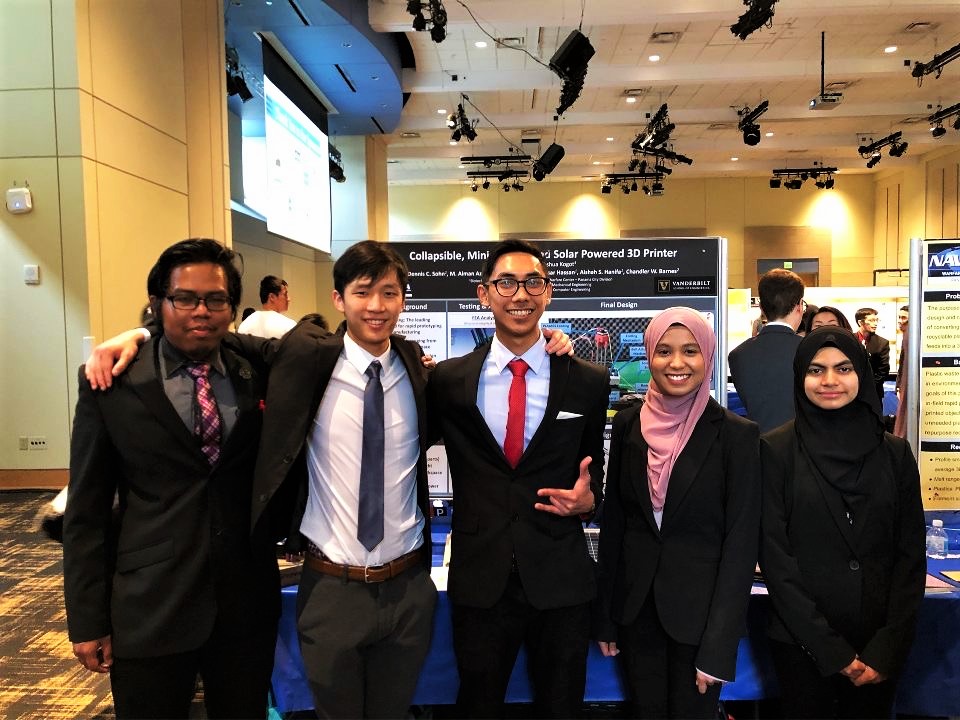
Skills I developed and used during this project:Technical:
- CAD (Creo and Inventor)
- FEA (ANSYS Workbench)
- Fabrication Methods and Materials (3D Printing, Machining, Laser Cutting)
- Electronic Motors, Instrumentation, and Programming (Arduino)
- Experiment Design
Non-Technical:- Leadership (Team Building, Strategy, Planning, Conflict Resolution)
- Communication (Presentations to advisers, faculty, and peers)
- Perseverence (too many late nights to count)
Links (click to view):